Slowly but surely, Honda is transitioning to electric vehicles. On Tuesday, the Japanese automaker announced the next step on this journey, some important news about its EV Hub in Ohio.
Gearing up to produce a new generation of Honda-developed electrics, the company is retooling three major manufacturing facilities in the Buckeye State. Honda’s Marysville Auto Plant, the East Liberty Auto Plant and Anna Engine Plant are all receiving significant upgrades to support flexible manufacturing. This means factories will be able to produce traditional combustion-powered, hybrid and electric vehicles all on the same assembly line. For instance, the Marysville facility currently has two production lines, though these will be consolidated into just one.
“There are not a lot of manufacturers that are producing EV models on a common ICE and hybrid production line,” explained Mike Fischer, executive chief engineer and Honda EV Hub lead in a one-on-one interview with EV Pulse. “I mean, there has been some, but in general, a lot of them are exclusive facilities.”
Aside from this news, Honda is also focusing on making its manufacturing facilities friendlier to both employees and the environment. Team member workflows have been analyzed and optimized to reduce unnecessary movements, which improves efficiency and reduces strain. These changes will bolster productivity and quality, but Honda is also working to reduce environmental impact. Future vehicles will incorporate a new Honda-developed aluminum that’s more recyclable, and engineers have developed a megacasting technology for building EV Intelligent Power Units, or IPUs (Honda lingo for battery cases).
Fischer explained that megacast IPUs will be made in two sections, front and rear, that then get joined together. Even though these battery housings are not “one and done,” that is, manufactured in a single time-saving, cost-reducing step, he said they still require far fewer individual components and less time to assemble.
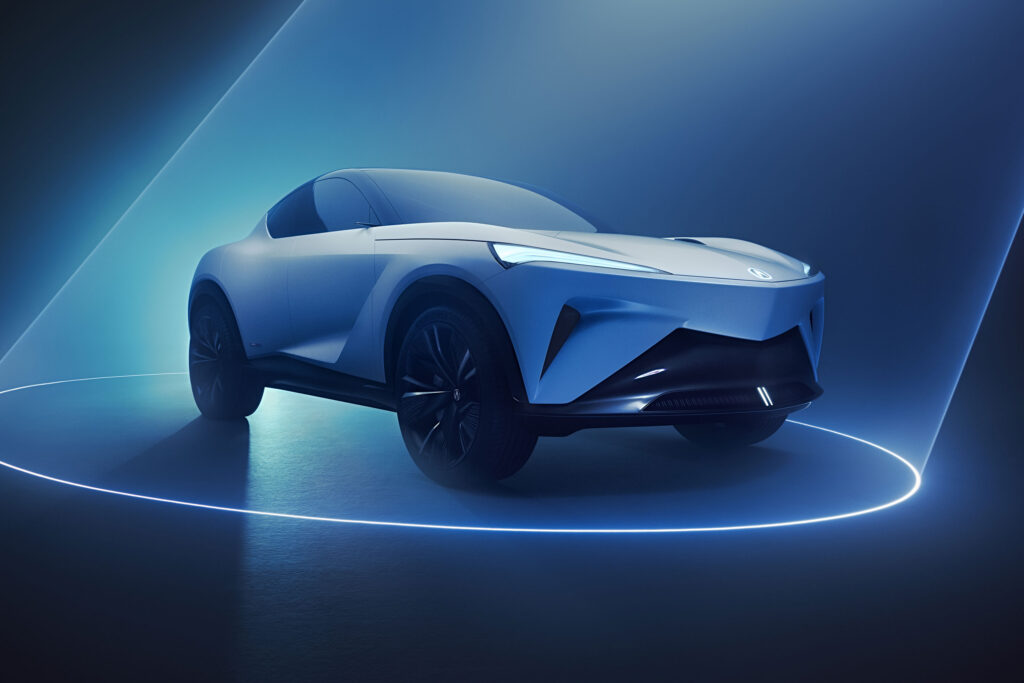
The main reason for employing this new manufacturing technique for IPUs is to efficiently build next-generation EVs, but there’s another aim. “The second purpose is for us to develop baseline knowhow for next-step activities for megacast applications,” said Fischer, “know-how that can be transferred for future applications as we move forward with vehicle development.” In short, this engineering exercise is also about learning, since the company has never done anything like this at such scale before
To make those megacast IPUs, Honda is installing six, 6,000-ton high-pressure die casting machines at its Anna Engine Plant, massive pieces of industrial equipment. Battery modules and other components will then be installed at the Marysville facility.
When asked about Honda’s new homegrown EV platform, Fischer said it’s intended to support vehicles like midsize SUVs, though he declined to cover any specifics about the architecture. The first vehicle to be built on this foundation will be the production version of the Acura Performance EV concept, which is expected to come out in late 2025.
Honda currently offers two all-electric SUVs built on GM’s Ultium battery platform – the Honda Prologue and Acura ZDX. The automaker is moving away from this partnership because, “Your ability to optimize not just the development spec but the manufacturing value chain is enormous. So, being able to do that is, I think, a distinct advantage, a game-changer for the future,” explained Fischer.
It will be interesting to see what the production version of the Acura Performance EV concept looks like, as well as the other electric vehicles made at Honda’s EV Hub in Ohio. Interestingly, the automaker has been building vehicles in Marysville since 1979 when it began manufacturing motorcycles there. Automobile production commenced in November of 1982, meaning, the company has been assembling cars in the U.S. for more than 40 years.